In the fast-paced world of industrial innovation, the demand for reliable, efficient, and precise motor testing solutions has never been greater. Whether you’re developing cutting-edge electric vehicles, optimizing aerospace systems, or refining industrial automation processes, the backbone of success lies in your ability to validate performance, durability, and efficiency. Enter hysteresis braking systems, dynamometers, clutches, and advanced motor test equipment—tools that redefine what’s possible in modern engineering.
🧲 HYSTERESIS BRAKES: THE SILENT WORKHORSE OF CONTROLLED MOTION
Hysteresis brakes are the unsung heroes of precision control. Unlike traditional friction-based brakes, these devices leverage magnetic hysteresis loss to generate torque without physical contact. This unique mechanism eliminates wear and tear, ensuring consistent performance over extended periods. Imagine testing a high-speed servo motor for a robotic assembly line—hysteresis brakes provide smooth, vibration-free deceleration, enabling engineers to simulate real-world conditions with unparalleled accuracy.
Applications span industries:
- Automotive: Testing EV drivetrains under variable loads.
- Renewable Energy: Validating wind turbine generators’ response to fluctuating wind speeds.
- Consumer Electronics: Ensuring whisper-quiet operation in precision devices like MRI machines.
📊 HYSTERESIS DYNAMOMETERS: WHERE DATA MEETS RELIABILITY
When it comes to measuring torque, speed, and power, hysteresis dynamometers stand in a league of their own. These systems use eddy current principles to create controllable loads, making them ideal for testing motors across their entire operational range. A key advantage? Their ability to maintain torque consistency even at near-zero speeds—a critical feature for applications like elevator motor validation or hybrid vehicle energy recovery systems.
Case in point: A leading EV manufacturer recently integrated hysteresis dynamometers into their R\u0026D process, reducing test cycle times by 40% while achieving sub-1% measurement uncertainty.
🔗 HYSTERESIS CLUTCHES: SEAMLESS POWER TRANSMISSION, REDEFINED
In scenarios requiring precise torque control without mechanical linkage, hysteresis clutches shine. By manipulating magnetic fields, these clutches enable slip-free engagement and infinite adjustability. https://www.openlearning.com/u/reesgotfredsen-stta32/blog/PoweringPrecisionDiscoverTheFutureOfHysteresisBrakesDynamometersAndMotorTestingSolutions packaging line where delicate vials must be handled with exact torque—hysteresis clutches ensure product integrity while minimizing downtime caused by mechanical fatigue.
🏭 MOTOR DYNAMOMETERS \u0026 TEST SYSTEMS: THE FUTURE OF QUALITY ASSURANCE
Modern motor dynamometers are no longer standalone devices but part of interconnected ecosystems. Advanced motor test systems now integrate hysteresis components with AI-driven analytics platforms, offering real-time insights into efficiency curves, thermal behavior, and failure prediction. For instance, a tier-1 aerospace supplier utilizes these systems to simulate 20 years of wing flap actuator stress in just 72 hours, dramatically accelerating certification timelines.
Key features of next-gen motor test equipment:
- Modular Design: Adaptable configurations for everything from micro-motors to 10MW industrial drives.
- Energy Recovery: Up to 90% of absorbed power can be fed back into the grid, slashing operational costs.
- IoT Connectivity: Remote monitoring and predictive maintenance capabilities via cloud-based dashboards.
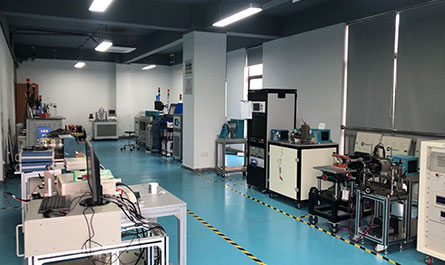
🌐 INDUSTRY 4.0 \u0026 BEYOND: WHY HYSTERESIS TECHNOLOGY MATTERS
As industries embrace smart manufacturing and sustainability goals, hysteresis-based solutions are becoming indispensable. Their non-contact operation aligns with zero-waste initiatives, while their compatibility with digital twins supports virtual prototyping—a game-changer for reducing physical testing costs.
Consider the rise of electric aviation: Startups designing eVTOL (electric vertical takeoff and landing) aircraft rely on hysteresis dynamometers to validate propulsion systems under extreme altitude and temperature simulations, ensuring passenger safety in uncharted operational envelopes.
🔧 CHOOSING THE RIGHT PARTNER: WHAT TO LOOK FOR IN A SUPPLIER
Not all motor test systems are created equal. When selecting equipment, prioritize vendors offering:
1. Customization: Tailored solutions for niche applications like underwater robotics or space-grade actuators.
2. Compliance: Built-in adherence to ISO, SAE, and IEC standards.
3. Lifetime Support: From installation to software updates, choose partners invested in your long-term success.
Electronics manufacturing automation : “Switching to [Your Company]’s hysteresis-based test rigs transformed our QC process. We’ve cut false failure rates by 65% and reduced energy consumption by 30%—all while meeting tightening EU efficiency regulations.”
🚀 TOMORROW’S CHALLENGES, TODAY’S SOLUTIONS
As motors grow smarter and applications more demanding, the fusion of hysteresis technology with machine learning and digital automation will define industry leaders. Imagine a world where self-optimizing test systems automatically adjust parameters based on live data streams, or where quantum computing enhances material selection for hysteresis discs. The future is here—and it’s magnetic.
Whether you’re pushing the boundaries of EV performance, pioneering sustainable energy solutions, or crafting the next generation of industrial robotics, hysteresis-driven motor testing systems provide the foundation for innovation. Precision cable winding ’t just meet standards—set them.
Ready to transform your testing capabilities? Let’s engineer excellence, one magnetic field at a time. 💡🔋